การเปลี่ยนปั๊มลมเก่าที่ประสิทธิภาพลดลง ด้วยปั๊มลมใหม่แบบอินเว อร์เตอร์
การเปลี่ยนปั๊มลมเก่าที่ประสิทธิภาพลดลง ด้วยปั๊มลมใหม่ จะเพิ่มประสิทธิภาพในการผลิตลมอัดเพิ่มขึ้นและลดค่าการใช้กระแสไฟฟ้าให้ลดลง

เนื่องจากในปัจจุบัน ยังมีลูกค้าที่ยังมีความเข้าใจผิดว่า ปั๊มลมยังไม่เสียหรือพัง ไม่ต้องซื้อใหม่ แต่ลูกค้าหาทราบว่า ปั๊มลมที่มีอายุการใช้งาน 7-10 ปี ประสิทธิภาพในการผลิตลมอัดจะตกลง ทำให้การใช้กระแสไฟฟ้ามากขึ้น และมีค่าซ่อมบำรุงสูง (งานโอเวอร์ฮอนล์)
ปั๊มลมรุ่นใหม่นั้นจะมีขนาดเล็กลงเพื่อให้ประหยัดพื้นที่ในการติดตั้ง แต่มีประสิทธิภาพในการผลิตลมอัดได้มากขึ้นดีขึ้น ทำให้ประหยัดพลังงานไฟฟ้ามากขึ้น

ปั๊มลมที่ใช้งานมานาน เมื่อคุณใช้งานจนครบอายุลูกปืน (ประมาณ ๕ ปี หรือ ๒๐,๐๐๐ ชั่วโมง) คุณต้องทำการโอเวอร์ฮอนล์ใหญ่ โดยเปลี่ยนแบริ่งและชุดซีลของลูกสกรู ทำการโอเวอร์ฮอนล์มอเตอร์ไฟฟ้าเปลี่ยนลูกปืน อาบน้ำยาวานิชและอบแห้ง ทำการเปลี่ยนสาย Hose ต่างๆ ทำการโอเวอร์ฮอนล์มอเตอร์พัดลม เปลี่ยนชุดแมกเนติก เปลี่ยนอะไหล่สิ้นเปลืองพวก กรองต่างๆ และน้ำมันเครื่อง ซึ่งรวมๆแล้วราคาสูงมาก อีกทั้งการทำโอเวอร์ฮอนล์ลูกสกรูอาจมีผลต่อประสิทธิภาพในการผลิตลมอัดให้น้อยลง ทำให้ปั๊มลมกินกระแสไฟฟ้ามากขึ้น


เมื่อคุณใช้งานโดยขาดการดูแลประจำวัน ประจำเดือน สภาพเครื่องจะเป็นแบบนี้
คุณมั่นใจมั้ยว่า เมื่อโอเวอร์ฮอนล์แล้วประสิทธิภาพจะเหลือเท่าไหร่
ในกรณีที่ปั๊มลมมีอายุการใช้งาน ถึง 7 ปี แสดงว่าจะต้องมีการโอเวอร์ฮอนล์มาแล้ว อย่างน้อย 1 ครั้ง ซึ่งระยะเคลียร์แล๊นซ์ของลูกสกรูอาจมากขึ้น ทำให้ประสิทธิภาพในการผลิตลมตกลงไป 5% - 10% หรือถ้าลูกค้าไม่ได้ทำการโอเวอร์ฮอนล์มาก่อน อายุของลูกปืนก็จะหมดไปทำให้ตัวโรเตอร์ของลูกสกรูเกิดการสึกหรอ ทำให้ประสิทธิภาพในการผลิตลมตกลงไป 5% หรืออาจมีการตกของลูกสกรูทำให้เกิดการเบียดของโรเตอร์ทำให้มอเตอร์ต้องกินกระแสไฟมากขึ้น
ปั๊มลมใหม่จะมีขนาดเล็กลงเพื่อลดพื้นที่ในการติดตั้ง แต่มีประสิทธิภาพสูงขึ้น โดยมีการพัฒนาให้ลูกสกรูทำลมได้มากขึ้น มอเตอร์เป็นแบบแม่เหล็กถาวร (Permanent magnet motor) ซึ่งมีประสิทธิภาพสูง ทอร์กสูง รองรับการสั่งงานจากอินเวอร์เตอร์ได้เร็วทันทีทันใด การกินกระแสไฟฟ้าน้อยลง
มอเตอร์ iPM นี้จะช่วยประหยัดพลังงานไฟฟ้าได้เพิ่มอีกถึง 4% และมีความทนทานสูง ดังจะเห็นได้ดังนี้



Integrated direct drive transmission
Energy saving vs. gear transmission
-
Integrated direct drive. element and motor share same rotor shaft
-
Coupling-free design > Minimal transmission losses
-
No coupling nor belts > Maintenancefree > Lower sevice costs >
Less downtime


OIL-COOLED iPM (INTERIOR PERMANENT MAGNET) MOTOR
No need for a ''drive side''bearing
-
No needed in our iPM design, rotor shaft directly coupled with the element
-
One less bearing > Less friction > Less Losses
Bearing on '' non-drive side'' greased for life
-
No need for re-greasing
-
Maintenance free > Lower service costs > Less downtime
-
No risk of forgetting to grease > No risk of motor failure
OIL-COOLED iPM (INTERIOR PERMANENT MAGNET) MOTOR
IP66 premium protection class
-
6 : Dust tight
-
6 : Protection against powerful water jets
-
Competitors have generally IP23 or IP55
No need for a motor cooling fan
-
Not needed thanks to the oil-cooling concept
-
Resulting in lower noise
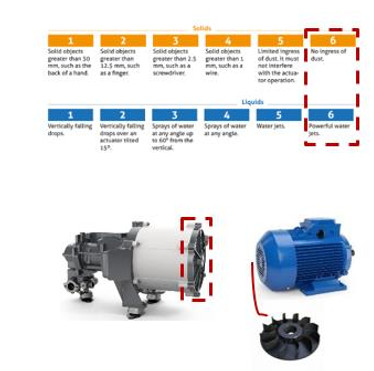
ในกรณีนี้เราจะทำตัวอย่างเปรียบเทียบค่าใช้จ่ายของกระแสไฟฟ้าระหว่างปั๊มลมใหม่แบบ iPMVSD กับปั๊มลมเก่า

เราจะเห็นว่า เมื่อประสิทธิภาพของปั๊มลมตกลงเพียง 5% เมื่อเทียบปั๊มลมใหม่กับปั๊มลมเก่า จะมีค่าใช้จ่ายกระแสไฟฟ้าต่างกันปีละ 313,428 บาท ซึ่งเป็นค่าใช้จ่ายที่ต่างกันสูงมาก ทั้งนี้ยังไม่นับรวมค่าซ่อมบำรุงในการทำการ โอเวอร์ฮอนล์สำหรับปั๊มลมเก่าอีก ทำให้เมื่อนับรวมค่าใช้จ่ายทั้งหมด จะเห็นว่าการซื้อปั๊มลมใหม่จะคุ้มกว่าการฝืนใช้เครื่องเก่าที่เสื่อมประสิทธิภาพ
หวังว่าบทความนี้จะมีประโยนช์ไม่มากก็น้อย สำหรับทุกท่านในการทำโครงการเปลี่ยนปั๊มลมใหม่ เพื่อให้โรงงานของท่านลดการใช้พลังงานลง เป็นการช่วยประเทศเราให้ลดการใช้พลังงานลงด้วยเหมือนกัน
นับถือ ลงชื่อวิฑูรย์ เจริญพานิช